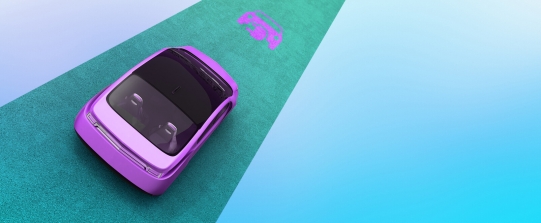
India’s e-mobility space has seen rapid growth driven by the demand for cleaner transportation and is estimated to have 10 million electric vehicles (EVs) on the road by 2030. As the country aims to establish an EV value chain in India, environmental and social risks plaguing the value chain worldwide pose a significant challenge to India’s sustainability goals in the Indian government’s vision for 2030. This Viewpoint analyzes these risks and recommends an integrated approach by stakeholders to proactively tackle the challenges to sustainability in the EV value chain.
INDIA’S E-MOBILITY SPACE
India currently faces severe pollution, with New Delhi being designated as the most polluted city in the world. Nationwide, an annual death toll of 2 million people is associated with air pollution. And, since according to New Delhi-based research and advocacy group Centre for Science and Environment, more than half of particulate pollutants in the air arise from emissions from two-, three-, and four-wheeled vehicles, this has created the demand for cleaner transport, with battery-powered EVs with zero “tailpipe” emissions emerging as the primary solution to the crisis. EVs have been hailed as clean vehicles that will transform mobility and significantly reduce transportation’s harmful impact on the environment. As India becomes more focused on sustainable alternatives for transportation, EVs have come to the fore.
The Indian government has recently launched encouraging policies such as Faster Adoption and Manufacturing of Hybrid and Electric Vehicles (FAME II) to increase the adoption of EVs, and the resulting increase in investors’ confidence has inspired a flurry of start-ups in the electric mobility space. These efforts are transforming India’s mobility landscape to the extent that Arthur D. Little (ADL) has forecasted that India’s EV industry will exceed sales of 10 million units by 2030, with an overall adoption rate of more than 30% across different vehicle classes, including two- and three-wheelers (see Figure 1).[1] In fact, ADL projects India to be among the top 10 EV markets globally by 2030. This is a significant step in India’s path to net-zero emissions by 2070.
To meet this demand, India is planning to set up an EV value chain in the country to reduce dependency on imports, specifically in battery manufacturing. Such infrastructure is essential, as dependence on imports exposes the country to risks due to geopolitical tensions, which run high in the case of raw materials for batteries and e-motors due to the concentration of resources and production capabilities in only a few selected countries.
In 2021, India’s first lithium reserve of 1,600 tons was discovered in Karnataka, after which the government announced that it will set up a lithium refinery in Gujarat to process battery-grade material. The country also has considerable reserves of manganese and graphite.
The Indian government announced the production-linked scheme (PLI) in May 2021 for advanced chemistry cell (ACC) battery storage manufacturing to promote domestic manufacturing of EV batteries. A few small players in India, such as Allox, are already building from scratch the cells required for EVs, along with large companies like Mahindra and Ola, which plan to establish their manufacturing facilities in the coming years. Currently, the actual battery value chain in India begins at the module and pack integration level, as this is the most accessible entry point into the battery business. The EV manufacturing space itself is already well established in India with the presence of multiple incumbent OEMs as well as new entrants, particularly in the booming market of electric two-wheelers. Tata is the market leader in electric passenger cars, according to Financial Express, with competition from MG, Hyundai, and Mahindra. At the end of the lifecycle, India is also building more and more capacity to recycle batteries.
As India steps forward on its path to electric mobility and establishes the EV value chain, it must lay a solid and sustainable foundation. Many countries have progressed significantly in the EV space but face questions about the environmental and social concerns surrounding the EV value chain. Permanent ecological damage from air, water, and soil pollution; poor waste management; and human rights issue due to child labor associated with different value chain steps have highlighted the dangers associated with irresponsible production of clean vehicles. On India’s journey toward electric mobility, sustainability should not be an afterthought, else the damage to the environment and society will be irreversible.
ASSESSING THE SUSTAINABILITY OF EV’S VALUE CHAIN
While EVs present a significant advantage in terms of sustainability over their internal combustion engine (ICE) counterparts when on the road, the environmental and social impacts of the “cradle-to-grave” value chain of EVs has raised concerns. These include mineral extraction, refining, the entire battery-production value chain, energy production, vehicle production, vehicle use phase, electricity generation for charging, and vehicle end-of-life recycling (see Figure 2).
EVs differ from conventional vehicles, particularly in the powertrain (electric drive and power electronics) and energy storage (battery). Of these systems, the battery has the highest value as well as the highest environmental risk. While battery EVs provide for “tailpipe” zero emissions, the battery itself comes with environmental, social, and governance (ESG) risks that are all too often neglected. Batteries are made from raw materials that are scarce and often mined in an unsustainable manner, have an unfavorable CO2 footprint in manufacturing, and are difficult to recycle. During the use phase, EVs are only as green as the electric energy used to charge them. Electricity is predominantly generated from burning fossil fuels and does little to decrease CO2 emissions.
India’s journey toward net-zero carbon emissions is long. And only by addressing the social and ecological footprint of the entire EV value chain, particularly the battery value chain, can the country get closer to its goal.
Next, we take a look at each step of the value chain and the associated challenges to society and the environment.
Mining: Social & environmental risks in sourcing raw materials
The lithium-ion (Li-ion) battery (i.e., NCM111) is the most commonly used battery in EVs. Mining operations across the globe for the many raw materials in these batteries, including lithium, cobalt, and nickel (see Figure 3), have been associated with water pollution, air quality deterioration, possible radioactive exposure, and other hazards. Mines for these resources are often in water-scarce areas, according to research by Massachusetts Institute of Technology, and require enormous amounts of water during the process.
Battery-mining operations have also represented some alarming cases of extreme human rights exploitation. For example, concerns have been raised over the mining of cobalt and associated risks to human rights. For countries like the Democratic Republic of Congo (DRC), where nearly half of the world’s cobalt reserves are found, investments in battery production could mean a boon to the economy. However, Chinese firms have aggressively acquired deposits in the DRC, with Bloomberg reporting that in 2017, China owned eight out of the 14 major DRC cobalt mines to support China’s growth in the EV battery space. Several incidents have occurred in DRC mines, which have been plagued by corruption and exploitation of locals. And due to governance failures, unregulated artisanal mines have emerged that have been linked to human rights violations that include child labor, high risks of injury, and increases in lung disease. There also have been a number of mine collapses due to a lack of health and safety regulations. According to a US Congressional hearing in 2022, as many as 40,000 child workers have been exploited in DRC mines. In a case filed in Washington, DC, USA, by a human rights firm on behalf of 14 DRC parents and children, the Guardian reported EV manufacturer Tesla to be among the defendants. The company and others were accused of aiding and abetting the death and severe injury of children working in cobalt mines in their supply chain. One of the primary allegations was that the companies involved were aware and were complicit in the forced labor of children.
Information regarding lithium mines has also come to light, with the New York Times reporting in May 2021 on a project known as “Lithium Americas,” which has drawn protests from a Native American tribe and environmental groups because it is expected to use billions of gallons of precious groundwater, potentially causing contamination that will exist for 300 years and leaving a giant mound of waste. There have also been reports that miners in Indonesia, one of the world’s biggest exporters of nickel, have requested permission from the government to dump their waste into the sea. And leakage from evaporation pools near Tibetan mines has led to dead fish and large animals floating down some of its rivers.
Apart from the minerals used in battery production, rare earth elements (REEs) like neodymium and dysprosium are required to make permanent magnets in electric motors. Without regulations and eco-friendly practices, these REE mines spew out partially radioactive sewage, and the processing liquid ponds can further increase the toxicity hazards to water, soil, and air through leakage, dust production, acid rain, eutrophication, and rain erosion.
Battery production: Impact on the environment
Batteries are at the core of EVs and claim 25%-35% of their total cost as well as impacting the vehicles’ range. Their production is a very energy-intensive process. According to Yahoo!, around 56% of the EV battery market is captured by China, where coal is the primary power source, leading to higher fuel-cycle emissions. Using data from a lifecycle assessment (LCA) in a 2022 Nature journal, ADL has deduced that the production of a 30 kWh battery in India can easily consume the CO2 equivalent of driving nearly 22,000 km in a typical crude oil–fueled car.
Despite efforts to make battery cell production greener, including the use of solar on plant roofs, cell production remains the largest greenhouse gas (GHG)–emitting step in battery production. These factories often do not prioritize energy efficiency when designing or evaluating the process setup. The battery manufacturing plant’s location affects the ambient temperature and the energy mix of their source electricity grid. Plants in warmer regions would require additional cooling facilities for specific steps in the battery-production process.
EV production: Environmental risks
Vehicle production is a resource-intensive process that pollutes the surroundings in various degrees. When it comes to EVs, the significant difference in components compared to ICEs is in the powertrain, which includes battery packs, traction motors, and power electronics. In 2020, the International Energy Agency (IEA) reported that 77% of the electric car market used permanent magnet traction motors made from expensive REEs, which produce a lot of waste and have various mining concerns (see Figure 4).
Unfortunately, the IEA reports that 85% of the supply of REEs is dominated by China, even though it has only an estimated 30%-40% of the total reserves. In 2010, China threatened to cut REE supply during a dispute with Japan, bringing to light the severity of the interconnection between geopolitical issues and critical resources. Furthermore, the unavailability of data regarding most of these Chinese plants means that the actual negative impact of REEs cannot be measured. A higher percentage of electricity from nonrenewable energy leads to a negative environmental impact. However, the situation is complex, considering that, for example, using hydroelectric power decreases the carbon footprint but in turn affects the water footprint. Huge distances between stakeholders in the manufacturing process also lead to more energy spent on transportation, which can further affect the environment.
Charging: Environmental impact based on source of electricity
Emissions during EV usage are impacted significantly by the method of electricity production. Considering the current electricity mix in India, the e-mobility space is merely shifting the GHG emissions from vehicle “tailpipe” to coal-fired power plants, resulting in poor air quality in their locations and affecting local communities and ecologies.
According to reports in Nature, using EVs in transportation reduces nitrogen oxide and particulate matter emissions, leading to better ambient air quality. However, relying on coal-fired power plants to power these vehicles can increase overall sulphur dioxide emissions by up to 18 times. The use of coal power substantially increases the ecological footprint of an EV over its lifetime, with just ~5% GHG reduction compared to the lifetime emissions from a typical gasoline car sold in India (see Figure 5).
End-of-life batteries: Challenges to recycling and second life
When incorrectly disposed, Li-ion batteries can leach out of landfills and pollute water sources and ecosystems. And although the lifespan of an EV battery is expected to exceed 10 years, toward the end of its useful life, it is expected to have less than 70% of its original capacity.[2] Replacing a battery will be cost-prohibitive toward the end of the battery’s useful life, essentially tying the vehicle’s life to that of its battery. Recycling can be profitable but it must be done correctly, as batteries contain toxic and carcinogenic substances. Li-ion battery recycling is still embryonic in India and requires significant scaling. Companies such as Tata Chemicals, Attero, and Lohum have embraced the recycling opportunity. Recycling, when done correctly, can give considerable relief to the end-of-life environmental impact and availability of raw materials and should therefore be considered a key priority.
The EV value chain is plagued by inefficiencies, negligence, and exploitation, resulting in harm to the environment and society — risking negating EVs’ benefits. Questions around the supposed “cleaner future” and its repercussions on the marginalized and the environment can be heard worldwide. With such a harsh price for a sustainable future, it remains to be seen whether such a path will be realistically sustainable. But what is the solution to this conundrum?
RETHINKING THE EV VALUE CHAIN: IMPLEMENTING 7 SUSTAINABLE SOLUTIONS
The following actions could help counter the ecological footprint across the EV value chain:
Policy-making perspective
-
Source raw material for batteries and e-motors. The social and environmental impacts of mines differ across countries and are worse in those with flourishing unregulated artisanal mines. Policies that penalize sourcing from unregulated businesses and instead incentivize responsible sourcing through trade agreements could in turn motivate unregulated mines to standardize and set regulations.
India does not have enough raw materials for battery production, so it must import the required materials. However, the industry and the government could focus on building refining infrastructure in India, which would also help ensure higher quality, resulting in a longer lifecycle of batteries. ADL has estimated that India must invest over US $10 billion to boost cell manufacturing and raw material refining to meet the local demand for Li-ion batteries by 2030. In addition, strategic trade deals and raw material sourcing will aid in creating a more controlled and cost-efficient EV value chain.
-
Sustain and protect different technologies. For a technology to take root, it requires government support from the start. As an example, battery-powered EVs have benefited from FAME II policies and have prospered due to subsidies and other forms of support. In the e-mobility space, technologies such as fuel cell EVs (FCEVs) use hydrogen, which has proved useful in heavy-duty vehicles, a space that battery-powered EVs (BEVs) have as yet been unable to penetrate. Such technologies complement existing technology and relieve the strain on select natural resources. Countries like Japan and Germany have started projects to assess the potential of FCEVs and provide them with similar incentives to BEVs. Germany is looking into transforming the industrial sector through hydrogen energy. In India, such a technology-open strategy could be essential to ensuring the prevalence of EVs in a sustainable manner.
-
Decarbonize electricity usage. Over recent years, the costs of renewable energy have fallen for both solar and wind energy. However, the reliability of these power sources is highly subjective to geography, which raises challenges to their adoption. A flexible system with intermittent solar, wind, and nonrenewable sources will ensure a reliable power supply. As Indian players establish their battery-production and EV manufacturing facilities, the government should incentivize them to install them closer to renewable power sources for a better energy mix.
-
Recycle EV batteries & motors. Second-life batteries will have to compete with new batteries with better and cheaper technology. There is a lack of successful use cases for reusing batteries, but recycling batteries is both scalable and profitable. E-motors should also be recycled to recover REEs.
As in the case of plastic, the government should shift the responsibility of recycling to the OEMs. Government can also establish requirements in battery making by setting targets on the amount of recycled raw materials used in batteries. In a recent example, the European Parliament is working on EU directives for more sustainable and ethical batteries. Its regulations include labelling batteries with their carbon footprint and having a minimum requirement of recycled raw materials. The directives also call for higher targets for battery recycling. Such government initiatives can significantly reduce the ecological footprint of the EV value chain.
Industry actionable
-
Research & development. Developing new battery chemistries such as sodium-ion, solid-state, nickel-cadmium, and other hybrids is also an option. Recently, there have been research developments in sodium-ion batteries, which are eco-friendly, cost-efficient, and capable of fast charging with much less environmental impact due to easier disposal and abundant raw materials. Hydrogen has been shown to be a clean fuel owing to its sustainable benefits and abundance. Producing EVs based on different technologies could also take the burden off select few natural resources. Several OEMs, such as Tesla, Honda, and BMW, are manufacturing e-motors that do not require one or more REE in order to reduce their dependency on China. And in the development of magnets, iron nitride super magnets are in the later stages of research and are expected to be an alternative to the current permanent magnets.
As electric mobility is adopted more widely, a growing number of batteries will be discarded in the coming years, and reuse and recycling of these batteries will be an essential concern. There is a need for batteries that can be easily dismantled, making the critical material within easily extractable, or being suitable for reuse in smaller appliances. Innovations in battery chemistry could also help in prolonging battery life. According to a report by the Guardian, a UK battery manufacturing start-up is using compression to reduce the need to bond components in a battery, making it easier to disassemble a battery pack for repairs, servicing, or repurposing. The company’s cofounder claims that making a battery serviceable in this way may extend a battery’s life by as much as 10 years. Similar methods could be used to extend battery life and make reuse and recycling more efficient.
-
Charging
-
Source renewable energy. There is a need to shift toward sourcing renewable energy for charging, and wind and solar power both are key contenders. This could be done by building strategic partnerships with renewable energy players. Wind energy is usually produced at farms far away from EVs and can be used to charge EVs at home at night. Solar energy, on the other hand, is produced during the day and could be decentralized by installing panels on building rooftops, making transportation costs significantly less by comparison. Solar panels also can be installed over office buildings, individual homes, and charging stations.
To understand the possibility of a charging stationed powered by solar panels, consider an EV charging station, which could be expected to consume 1,000 kWh units of electricity per day. The average power generation by 1 kW of solar panel in India is 4 kWh, hence 250 solar panels will be required to run the EV charging station. Since it requires 100 sq. ft. of solar panels for 1 kW, that means it would require 25,000 sq. ft. to set up these panels. The Economic Times reported that the minimum area for a charging station is could be as low as 100 sq. ft.
Therefore, powering charging stations with solar energy would significantly impact the land necessary to provide services. However, office and home rooftops could be ideal places to install these panels and provide an opportunity to charge vehicles at office parking lots or at users’ homes. A four-wheeled vehicle with a battery capacity of 30.8 kWh and a maximum range of 312 km would require 7.7 KW solar panels for full charge in a day. Two-wheelers will require fewer panels owing to their smaller batteries.
-
Smart grid control. Smart charging through V1G and V2G and similar technologies provides the ability to modify the charging time and rate dynamically and allows bidirectional charging. Vehicles connected to the grid provide storage capability to the grid and help in managing peak-hour requirements, making charging stations more ecologically efficient.
-
-
Integrated value chain. The EV value chain is replete with social and environmental risks, but the electric mobility industry and policy makers in India have the opportunity to collaborate across an integrated value chain to implement sustainable solutions, allowing for information sharing across stakeholders for transparent and innovative decision-making (see Figure 6). For example, battery manufacturing could be done with recycling and reuse in mind, making designs easy to dismantle and modify. Recycling plants could be situated closer to OEMs to decrease the cost of extracted materials and ensure a consistent supply. Most EVs are Internet of Things (IoT)-enabled, which allows for tracking the overall performance throughout their use, which could provide critical data regarding battery health and performance to be shared across the value chain for improved technology and production.
Conclusion
India’s path to a sustainable EV value chain
Policy-making and industry initiatives can direct the growth of the EV value chain in India toward a sustainable path. These actions can establish a strong and sustainable foundation for producing clean vehicles, contributing to India’s ambition of zero emissions and countering severe health hazards caused by pollution. The following steps could be taken to achieve this:
-
Regulate sourcing of raw materials and initiate policies to penalize raw materials not sourced responsibly.
-
Conduct research in various technologies to make batteries with chemistries, ease the recycling process, and make charging more efficient.
-
Increase share of green energy in EV production and charging and decarbonize electricity generation by establishing renewable power plants and installing panels over rooftops of buildings for localized production and distribution to optimize costs and energy efficiency.
-
Encourage recycling of EV batteries and e-motors to obtain essential raw materials from discarded batteries and produce sustainable and ethical batteries.
-
Integrate the EV value chain to promote information sharing and enable smart and sustainable solutions.
Notes
[1] Maitra, Barnik Chitran, et al. “Unlocking India’s Electric Mobility Potential.” Arthur D. Little Report, August 2022.
[2] Mrozik, Wojciech. “Environmental Impacts, Pollution Sources and Pathways of Spent Lithium-ion Batteries.” Energy & Environmental Science, Vol. 12, December 2021.